تاثیر هدفمندی یارانهها بر صنایع انرژیبر
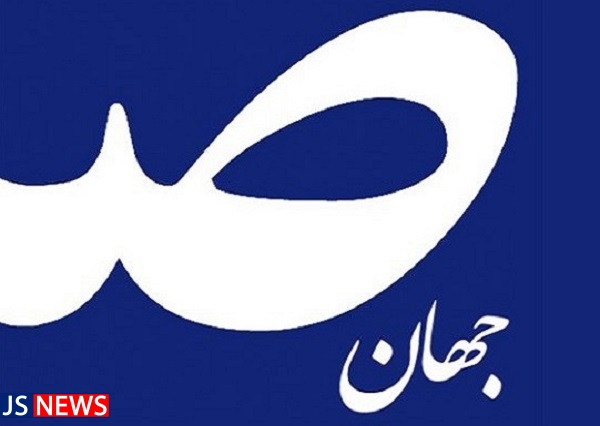
الهه رحیمدوست * سیاست هدفمندسازی یارانهها که با هدف کاهش مصرف انرژی و اجرای هرچه بهتر عدالت در کشور به مرحله اجرا درآمد، به دلیل تغییر در قیمت حاملهای انرژی، در بسیاری از بخشهای اقتصادی کشور تبعاتی را به دنبال داشته است. از آنجا که بخش فولاد و محصولات فولادی با توجه به انتخاب نحوه تولید در کشور فرآیندی انرژی بر است، بالطبع تاثیرپذیری زیادی را از اجرای این قانون پذیرفته است و هزینه تمامشده فولاد در کشور افزایش یافته است. این موضوع زمانی اهمیت دوچندان پیدا میکند که دولت در عمل به تعهدات خود مبنی بر پرداخت سهم بخش تولید از محل اجرای این قانون سر باز زده است. هرچند که افزایش قیمت ارز توانسته بخش زیادی از این هزینهها را برای تولیدکننده جبران کند، اما بخش خصوصی فعال در این حوزه بیشتر از بقیه بخشهای تولیدی دولتی متحمل هزینه شدهاند. ازاین رو، به منظور جلوگیری از کاهش قدرت رقابتپذیری ایران در عرصه بینالمللی و صادرات فولاد، برخی راهکارها ازجمله تغییر در روشهای تولید فولاد در کشور، افزایش حمایتهای دولتی از بخش خصوصی فعال در این بخش، کاهش مداخلات دولت در بازار فولاد کشور، حمایت از سرمایهگذاریهای خارجی، تعیین استراتژی توسعه فولاد با محوریت انرژی و آلودگی کمتر و… پیشنهاد میشود.
نقش انرژی در تولید فولاد
بخش صنعت پس از بخش خانگی و حملونقل ازجمله بخشهای پرمصرف انرژی به حساب میآید. در میان صنایع موجود در کشور، بخش صنایع معدنی سهم قابلتوجهی از مصرف انرژی در کشور را به خود اختصاص داده است. در این میان صنعت فولاد ازجمله صنایع معدنی انرژیبر، سرمایهبر و نیازمند تکنولوژی بالا است. ازاین رو، به دلیل بالا بودن سهم انرژی و تکنولوژی در تولید و قیمت تمامشده فولاد، رقابت در عرصه جهانی نیازمند توجه به نوع تکنولوژی تولید و بهینه کردن مصرف انرژی در انواع روشهای تولیدی است. بنابراین نگاهی به میزان مصرف انرژی در هر یک از بخشهای تولیدی صنعت فولاد و مقایسه آن با استانداردهای جهانی میتواند راهکارهای بهتری را در راستای رسیدن به مصرف استاندارد برای برنامهریزان و سیاستگذاران کشور تبیین کند. باتوجه به اهمیت موضوع، ابتدا به بیان روشهای مختلف تولید فولاد در کشور اشاره میشود. دلیل این بررسی آشنایی با پروسه تولید و مراحل مصرف انرژی در این صنعت است.
یکی از روشهای تولید فولاد استفاده از روش کوره بلند است. در این روش پس از آمادهسازی سنگآهن که در محل معادن سنگآهن کشور صورت میپذیرد، به کمک کُک، کلوخ و آهک، احیا و تصفیه صورت میگیرد. در این فرآیند، مواد یادشده وارد کوره بلند میشوند و با استفاده از دمش اکسیژن، فرآیند احیا انجام میپذیرد؛ این در حالی است که محصول به دست آمده از کوره بلند حاوی ۳ تا ۵/۴ درصد کربن است که به منظور تهیه فولاد باید درصد کربن آن کاهش یابد؛ ازاین رو، با ورود محصول کوره بلند به کوره اکسیژن، فولاد کوره اکسیژن با میزان کربن بین ۰ – ۵/۱ درصد به دست میآید که پس از انجام برخی عملیاتها روی آن، فولاد خام تهیه میشود. برخی تحقیقات نشان داده است که حدود ۶۶ تا ۶۷ درصد از تولید فولاد خام در جهان به روش کوره بلند انجام میشود.
در روش دیگر که به روش احیای مستقیم معروف است معمولا سنگآهن در حالت جامد به وسیله گاز یا کک احیا شده و تبدیل به آهناسفنجی میشود و پس از آن با استفاده از دو فرآیند میدرکس یا اچ.وای.ال احیای مستقیم شده و به فولاد تبدیل میشود. در این روش هرچه میزان مصرف قراضه در فرآیند تولید بیشتر باشد، به همان میزان مصرف انرژی کاهش مییابد. این در حالی است که مشاهدات نشان میدهد دلیل منابع فراوان و ارزانقیمت گاز در کشور استفاده از روش احیای مستقیم یا قوس الکتریکی بسیار شایع است. در این روش هزینه انرژی مشتمل بر گاز طبیعی و الکتریسته است که تاثیر به سزایی در هزینه تمامشده تولید فولاد خام دارد.
شکلگیری ساختار هزینه در صنعت فولادسازی کشور به گونهای است که به دلیل مزیت نسبی کشور در برخورداری از سنگآهن، ایران در مراحل تولید فولاد از سنگآهن به عنوان اصلیترین نهاده تولید استفاده میکند. این در حالی است که در جهان شاهد توسعه کاربرد آهن قراضه به عنوان اصلیترین نهاده تولید فولاد هستیم. از نکات حائز اهمیت این است که سهم بالای حمل نهاده، درنتیجه عدم توسعهیافتگی زیرساختهای حملونقلی در کشور است؛ همچنین سهم مواد کمکی، الکترودها و نسوزها، فروآلیاژها نیز به دلیل وابستگی وارداتی در هزینه تولید بسیار بالاست. یکی دیگر از موارد مهم قابل ذکر، بالابودن سهم هزینههای نیروی کار ناشی از بهرهوری پایین نیروی کار در کشور در مقایسه با تولید فولاد به روش قوس الکتریکی در جهان است. بنابر آمار منتشر شده در سال ۲۰۲۰، کمتر از ۹ درصد تولید فولاد ایران به کوره بلند اختصاص دارد و بیش از ۹۱ درصد تولید آن توسط کورههای قوس الکتریکی انجام میشود. هرکدام از روشهای یادشده مزایا و معایب مختص به خود را دارند ولی انتخاب نهایی روش تولید، به پارامترهای مختلفی بستگی دارد.
روشهای کاهش هزینه تولید
مواد اولیه و قیمت انرژی از اثرگذارترین پارامترها در این حوزه به شمار میآیند. زغالسنگ و کُک را میتوان از مواد اولیه اصلی در تولید فولاد به روش کوره بلند نام برد، اما ایران از منابع غنی زغالسنگ برخوردار نیست تا بتواند آن را به کُک تبدیل کند. استفاده از کُک وارداتی علاوه بر مشکلات تامین، به دلیل قیمت بالای آن به لحاظ اقتصادی، زیاد مقرون به صرفه نیست، البته برخی کارشناسان بر این باورند که اگر اکتشافات تکمیلی انجام شود قطعا به ذخایر مناسبی از زغالسنگ دست پیدا خواهیم کرد، اما تحقق این امر مستلزم سرمایهگذاری بالا و تکمیل فعالیتهای اکتشافی دارد؛ بنابراین وجود منابع گاز طبیعی فراوان و به نسبت ارزان و همچنین ذخائر عظیم سنگآهن مرغوب از مهمترین دلایل توسعه روش کورههای قوس الکتریکی در ایران به شمار میآید. باتوجه به مطالب یادشده میتوان گفت تاثیر انرژیبر هزینه تولید هر تن فولاد و استفاده بهینه از انرژی و بازیابی آن نقش موثر و تعیینکنندهای در کاهش قیمت تمام شده هر تن فولاد تولیدی دارد، به طوری که در روشهایی که بازیابی در حد بالایی صورت میگیرد، این امر نقش بهسزایی در کاهش هزینه خواهد داشت. تا جایی که سهم هزینه الکتریسیته در تولید به روش کوره بلند حدود پنج درصد و در روش احیای مستقیم، حدود ۱۰ درصد است. درحالی که سهم هزینه گاز در تولید به روش کوره بلند تقریبا ناچیز و قابل صرف نظر است ولی در روش احیای مستقیم به حدود ۱۱ درصد میرسد.
با توجه به مباحث یادشده، میتوان استنباط کرد که روش تولید فولاد در کشور، روشی انرژی بر است و از اینرو، انتخاب هرگونه استراتژی در تعیین قیمت حاملهای انرژی میتواند بر میزان سوددهی این صنعت و قیمت تمامشده محصولات فولادی تاثیر مستقیمی داشته باشد که طبیعتا این موضوع میتواند در بازارهای رقابتی و صادراتی جایگاه کشور را دچار نوسان کند. بر اساس برخی مطالعات صورت گرفته توسط سازمان بهینهیابی مصرف سوخت، صنعت فولاد پُرمصرف ترین صنعت انرژی بر کشور است. برای تولید هر تن فولاد، بدون در نظر گرفتن فرآوری مواد اولیه و جابه جایی و با احتساب ضریب نیروگاهی برای تامین انرژی الکتریکی، حدود ۶۵۰ تا ۷۵۰ مترمکعب گاز طبیعی مورد نیاز است. این میزان حدود هفت برابر انرژی مورد نیاز برای تولید سیمان است. با در نظر گرفتن قیمت محصولات فولادی در حدود ۵۰۰ دلار بهازای هر تن و هزینه بینالمللی انرژی ۲۰ سنت (میانگین برق و گاز مصرفی)، در حال حاضر حدود ۳۰ درصد بهای فروش به همین دلیل در ۱ فولاد، هزینه انرژی مصرفی است.
میزان اثرپذیری صنعت فولاد از سیاستگذاری بخش انرژی
اجرای سیاستگذاریهای دولت اثرات بسیار متفاوتی بر عملکرد بخشهای مختلف اقتصادی در کشور میگذارد. یکی از سیاستهایی که طی یک دهه اخیر شاهد اجرای آن در کشور بودهایم، اجرای قانون هدفمند کردن یارانهها به منظور بهینه کردن مصرف انرژی و حفظ عدالت در برخورداری دهکهای مختلف درآمدی در استفاده از یارانه تعلق گرفته به بخش انرژی در کشور است. باتوجه به اینکه صنعت فولاد یکی از صنایع به شدت انرژی بر است، ازاین رو، اجرای قانون هدفمند کردن یارانهها بر قیمت تمام شده این بخش از صنعت، اثرگذار است. وجود ارتباطات پسین و پیشین این صنعت با سایر صنایع موجب میشود تا تغییر قیمت فولاد آثار مهمی بر سایر بخشهای اقتصادی و صنعتی کشور داشته باشد. این در حالی است که یکی از مهمترین موضوعات در اجرای قانون هدفمندی یارانهها، اجرای سیاستهای بازتوزیعی و جبرانی منابع حاصل از اجرای این قانون بوده است. به نحوی که بر اساس قانون مذکور، سهم خانوارها، تولید و دولت از منابع پیادهسازی این قانون به ترتیب ۵۰ ،۳۰ و ۲۰ درصد بوده است، اما بررسی عملکرد دولت طی سالهای اجرای این قانون نشان میدهد که در بسیاری از سالها سهم بخش تولید از محل اجرای این قانون نادیده گرفته شده و یا در برخی از سالها تحقق سهم ۳۰ درصدی بخش تولید به طور کامل تحقق نیافته است. بنابراین میتوان گفت یکی از بخشهایی که از جانب اجرای قانون هدفمندی یارانهها بیشترین آسیبپذیری را داشته بخش تولید کشور است، زیرا یکی از مزیتهای تولید در کشور، انرژی ارزانقیمت در این بخش بوده است که متاسفانه با اجرای این قانون میتواند بیشترین آسیب را متحمل شود.
در این میان انتظار میرود بخش تولید فولاد که در میان دیگر صنایع از انرژیبری بالایی برخوردار است، اثرپذیری بالایی نیز از اجرای این سیاست داشته باشد. بنابراین باتوجه به اهمیت موضوع در این بخش از گزارش، با تکیه بر آمار در دسترس، میزان تاثیر تغییر قیمت حاملهای انرژیبر صنعت فولاد کشور تبیین میشود. قبل از هر چیز آگاهی از سهم هر یک از منابع انرژی در روند تولید صنایع آهن و فولاد میتواند اهمیت تامین انرژیهای مختلف را به منظور تولید فولاد در کشور بیش از پیش روشن کند. سهم مصارف انرژی در صنایع آهن و فولاد نشان میدهد که سهم مصرف گاز طبیعی ۴ برابر سهم انرژی الکتریسیته در این صنایع است و سهم کُک به عنوان منبع انرژی سوم از بقیه منابع کمتر است. باتوجه به آمار در دسترس، به رغم پایینتر بودن سهم برق مصرفی در این صنعت، در مقایسه با سهم گاز طبیعی، میزان برق مصرفی صنعت فولاد کشور در سال ۱۳۹۸ در این بخش مورد بررسی قرار میگیرد.
جدول ۱: ظرفیت و مصارف برق کشور در سال ۹۸
شاخص |
واحد اندازهگیری |
مقدار |
ظرفیت نیروگاههای کشور |
مگاوات |
۸۳۴۷۸ |
کل مصرف |
میلیون کیلووات ساعت |
۲۷۱۹۰۱ |
کل مصرف صنعت |
میلیون کیلووات ساعت |
۹۴۴۷۰ |
مصرف زنجیره فولاد |
میلیون کیلووات ساعت |
۳۰۸۲۵ |
با توجه به بررسیها، ظرفیت و تولید برق نیروگاههای کشور، مشاهده میشود که از ۸۳۴۷۸ مگاوات تولید برق در کشور در سال ۱۳۹۸، ۲۷۱۹۰۱ میلیون کیلووات بر ساعت آن به مصرف رسیده است که در این میان بخش صنعت با مصرف ۹۴۴۷۰ میلیون کیلووات ساعت ۳۵ درصد از میزان برق مصرفی را به خود اختصاص داده است. این در حالی است که میزان مصرف زنجیره فولاد از برق مصرفی بخش صنعت حدود ۳۳ درصد است که از این مقدار ۶۸ درصد سهم بخش تولید فولاد و ۱۲ درصد سهم تولید آهن اسفنجی است. بنابراین انتظار میرود به منظور تحقق چشمانداز ۲۰ ساله کشور مبنی بر تولید ۵۵ میلیون تن فولاد خام، سالانه نیاز به تولید ۴۵۹۰۵ میلیون کیلووات ساعت برق در کشور باشد که این میزان معادل حدود ۴۹/۱ برابر مقدار برق فعلی فولاد (۳۰۸۲۵ میلیون کیلووات ساعت) خواهد بود. در زمینه میزان گاز مصرفی در صنعت فولاد کشور نیز بر اساس آمار موجود و در دسترس مشاهده میشود که ۱۳۱۷۹ میلیون مترمکعب گاز در کل زنجیره تولید فولاد در سال ۱۳۹۸ مورد استفاده قرار گرفته است.
مطابق بررسیها، در فرآیند تولید فولاد در کشور، حجم گاز مصرفی به منظور تولید آهن اسفنجی بیش از بقیه مراحل است. همچنین بر اساس آمار موجود، باید گفت به منظور تحقق چشمانداز ۲۰ ساله کشور، در سال ۱۴۰۴ برای تولید ۵۵ میلیون تن فولاد خام در کشور، سالانه حدود ۹۵/۱۸ میلیارد مترمکعب گاز مورد نیاز صنعت فولاد است که این میزان معادل ۴۳/۱ برابر مقدار گاز فعلی (۱۳۱۷۹ میلیون مترمکعب) مورد مصرف در صنعت فولاد کشور است. اعمال سیاستهای اقتصادی ازجمله اجرای قانون هدفمندسازی یارانهها با تغییر در نرخ تعرفه مصرفی حاملهای انرژی میتواند در میزان سوددهی آن بخش اثرگذار باشد؛ ازاین رو، با توجه به اینکه در تفکیک مصارف انرژی صنایع آهن و فولاد، سهم خش گاز طبیعی در مقایسه با دیگر انرژیهای به کار رفته در این صنعت بالاتر است، در این بخش به مقایسه تغییر قیمت گاز طبیعی در قبل و بعد از اجرای هدفمندی یارانهها خواهیم پرداخت.
رشد ۲۷۱ درصدی تعرفه گاز مصرفی
با توجه به آمار در دسترس، تعرفه گاز مصرفی برای کارخانجات فعال در عرصه تولید فولاد خام، از سال ۱۳۸۹ تاکنون از رشدی بالغ بر ۲۷۱ درصد برخوردار بوده است، به نحوی که از ۷۰۰ ریال در سال ۱۳۸۹ به ۲۶۰۰ ریال در سال ۱۳۹۹ افزایش یافته است. این موضوع ضرورت بهبود تکنولوژی و تغییر در روش تولید فولاد از روشهای نسبتا با انرژیبری بالا به روشهای با انرژیبری پایین را طلب میکند. این موضوع در حالی مطرح است که بر اساس آمار موجود میزان مصرف گاز طبیعی در زنجیره تولید فولاد در سال ۱۳۹۵ معادل ۴/۸۸۴۶ میلیون مترمکعب در سال و در سال ۱۳۹۸ معادل ۱۳۱۸۰ میلیون مترمکعب در سال بوده که این رقم به معنی رشد حدود ۴۹ درصدی در میزان استفاده از گاز طبیعی در خط تولید فولاد کشور است.
بنابراین میتوان گفت، اجرای قانون هدفمندسازی یارانهها به خودیخود میتواند منجر به افزایش قیمت تمامشده تولید فولاد در کشور شود که این موضوع منجر به کاهش قدرت رقابتپذیری کشور در عرصه بینالمللی خواهد شد (این در حالی است که یکی از ضرورتهای اسناد بالادستی کشور به منظور پیمودن روند رو به جلوی توسعه، کاهش وابستگی به صادرات نفت و در مقابل افزایش صادرات غیرنفتی است. از این رو، گسترش و تقویت صادرات فولاد میتواند یکی از زمینههای رشد اقتصادی و دستیابی به اهداف تعیینشده را فراهم آورد)، اما از آنجا که قیمت ارز در کشور از رشد قابل توجهی برخوردار است، توانسته تا حد بسیار زیادی مانع از کاهش توان رقابت ایران در عرصه تولید و در نهایت صادرات شده که این موضوع درخصوص کارخانجات دولتی بیشتر قابل رویت است، زیرا کارخانجات بخش خصوصی به دلیل عدم توانایی در ورود تکنولوژی و یا تامین هزینهها، قادر به ادامه حیات اقتصادی خود نبودهاند. مطابق نظر برخی کارشناسان و صاحبنظران در این حوزه، میتوان به این نکته اشاره کرد که هرچند اتخاذ روشهای مناسب به منظور جلوگیری از هدررفت منابع گاز و برق در کشور بسیار مورد استقبال کارخانجات فعال در این حوزه است، اما در وضعیت فعلی، حتی با وجود اعمال تعرفههای بالاتر در قیمت حاملهای انرژی، چنانچه دولت در مقوله قیمتگذاری بخش فولاد مداخلهای نداشته باشد، شاهد سوددهی کارخانجات تولید فولاد در کشور خواهیم بود. برخی راهکارها به منظور تقویت بخش فولاد کشور به شرح زیر ارائه میشود.
حمایت تغییر در روشهای تولید فولاد در کشور
با توجه به اینکه بخش عظیمی از تولید فولاد کشور با روش قوس الکتریکی در حال انجام است و با عنایت به اینکه روش یادشده به علت وجود منابع انرژی ارزان در کشور بسیار مورد استقبال بوده، از این رو، پیشنهاد میشود به دلیل پایانپذیر بودن و محدودیت منابع و همچنین جلوگیری از هدررفت منابع انرژی، با بهبود تکنولوژیهای موجود زمینههای لازم برای تغییر در روش تولید فولاد در کشور فراهم شود. این در حالی است که سهم انرژی در قیمت تمامشده محصولات فولادی بسیار بالاست. بنابراین تغییر در روش تولید فولاد میتواند با کاهش قیمت تمامشده، قدرت رقابت تولیدات داخل را در عرصه خارجی افزایش دهد.
افزایش حمایتهای دولتی از بخش خصوصی فعال در این بخش
همانطور که در متن گزارش نیز تا حدودی به آن اشاره شد، وجود حمایتهای دولتی از بخش فولاد توانسته کارخانجات وابسته را تا حدودی از تبعات اجرای سیاستهای اقتصادی (ازجمله هدفمندسازی یارانهها و افزایش قیمت حاملهای انرژی) مصون نگه دارد، اما بخش خصوصی فعال در عرصه تولید فولاد، با توجه به استراتژی برخی نهادهای ذیربط ازجمله صنایع و معادن در صدور پروانههای تولیدی و همچنین بالا بودن هزینههای تولید نتوانسته متناسب با ظرفیتهای تولید نصب شده اقدام به فعالیت کند. بنابراین پیشنهاد میشود دولت با پرداخت سهم بخش تولید از محل اجرای قانون هدفمندسازی و یا کاهش تعرفههای وارداتی در مواجهه با بحرانهای کاهش یا افزایش قیمتهای جهانی فولاد و… به رونق فعالیت بخش خصوصی در زمینه فولاد کمک کند.
کاهش مداخلات دولت در بازار فولاد کشور
به عقیده برخی کارشناسان وجود مداخلات دولت در سیستم قیمتگذاری و تنظیم بازار فولاد موجب برخی اختلالات در تعیین قیمت و به تبع آن، تغییر در میزان سوددهی واحدهای تولیدی مربوطه میشود. ازاین رو، پیشنهاد میشود دولت با کاهش مداخلات خود در زمینه قیمتگذاری فولاد و محصولات آن، مانع از کاهش سوددهی کارخانجات تولید فولاد شود و درنتیجه تعیین قیمت را به تعادل عرضه و تقاضا در بازار محول کند، زیرا اعمال سیاستهایی همچون اصلاح قیمت حاملهای انرژی، هزینه تمامشده فولاد در کشور را افزایش داده است، این در حالی است که افزایش نرخ ارز و صادرات محصولات تولیدی توانسته تا حدود زیادی این هزینهها را پوشش دهد. حال چنانچه دولت در قیمتگذاری فولاد مداخله کند، میتواند منجر به عدم سوددهی فعالیت فولادسازان در کشور شود.
حمایت از سرمایهگذاریهای خارجی
با توجه به محدودیتهای داخلی درخصوص تامین منابع مالی لازم جهت انجام سرمایهگذاریهای جدید و یا تکمیل پروژههای در دست ساخت در صنعت فولاد، یکی از راهکارهایی که میتواند تا حد زیادی برای رفع این کمبودها موثر واقع شود، حمایت از سرمایهگذاران خارجی به منظور سرمایهگذاری در این بخش از صنعت است. همچنین از آنجا که کشور همواره با انواع تحریمهای خارجی مواجه بوده، امکان انتقال فناوری به منظور توسعه هرچه بهتر روشهای تولید در این صنعت در کشور مقدور نبوده است، این در حالی است که ورود سرمایهگذار خارجی میتواند راهگشای انتقال فناوری در صنعت فولاد به کشور باشد.
تعیین استراتژی توسعه فولاد با محوریت انرژی و آلودگی کمتر
وجود کمبودها و محدودیت در منابع کشور، برنامهریزان را همواره به این موضوع رهنمون میکند که استفاده از این منابع (خصوصا آب و برق) باید بر اساس استراتژی درست و حسابشده صورت پذیرد. از اینرو، با عنایت به اینکه صنعت فولاد کشور یکی از منابع انرژیبر است و بعضا هدررفت منابع آبی در این صنعت غیرقابل چشمپوشی است، به همین دلیل پیشنهاد میشود با تعیین استراتژی کشور در بخش صنعت فولاد کشور و اولویت قرار دادن محدودیت منابع و لزوم کاهش آلودگی (در حوزه احداث واحدهای جدید و یا نحوه تولید فولاد در هر یک از واحدهای فعال) در این صنعت، مانع از هدررفت منابع در کشور باشیم.
*پژوهشگر اقتصادی
اخبار برگزیدهیادداشت
لینک کوتاه :