راهبردهای مدیریت مصرف گاز در صنایع فولاد و آهن کشور/سناریوهای گازی تا افق ۱۴۲۰
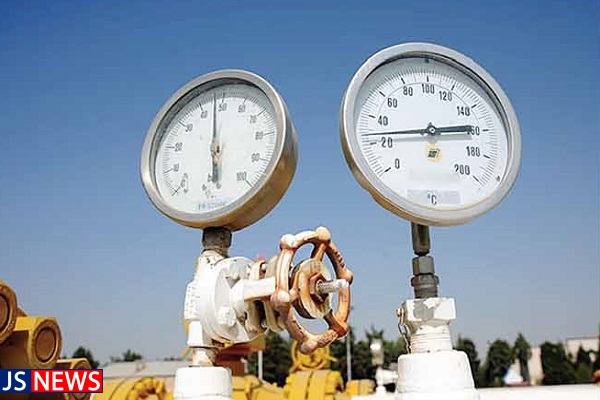
به گزارش جهان صنعت نیوز: زنجیره فولاد یکی از بخشهای اصلی مصرفکننده گاز در عرصه صنعت شمرده میشود. صنعت فولاد هم اکنون حدود ۱۱ میلیارد مترمکعب گاز در سال مصرف میکند که پیشبینیها حاکی از آن است که مصرف گاز آن در ۵ سال آینده ۲ برابر میشود. روند فزاینده مصرف گاز این صنعت با توجه به ناترازی گازی کشور در سالهای آینده، یکی از مشکلات اساسی پیشروی صنعت فولاد کشور به شمار میرود. با تداوم روند موجود مصرف گاز، برای تحقق تولید ۵۵ میلیون تن فولاد تا افق سال ۱۴۰۴، این صنعت به مصرف ۲/۱۹ میلیارد مترمکعب گاز در سال نیاز دارد. این در حالی است که صنعت فولاد کشورمان با ظرفیت کاهش معادل ۱۲ میلیون مترمکعب گاز طبیعی در روز، ظرفیت صرفهجویی مصرف گازی بالغ بر ۳۰ درصد را دارد. نظر به زیانهای عدیدهای که تداوم روند موجود مصرف گاز در این صنعت ایجاد میکند، بر اساس این گزارش راهکارهایی از قبیل اصلاح و افزایش تعرفه سوخت واحدهای مصرفکننده بالاتر از معیار مصرف انرژی برای ترغیب واحدها به صرفهجویی مصرف گاز، صرفهجویی مصرف انرژی با سرمایهگذاری در بهبود بازده انرژی برای تولید فولاد در کوره قوس الکتریکی و جلب همکاریهای بینالمللی برای افزایش سرمایهگذاری در راستای ارتقای فناوری تولید فولاد در کشور پیشنهاد میشود.
امروزه اهمیت صنعت فولاد به دلیل نقش مهمی که در تکمیل زنجیره تولید صنایع مهم و کلیدی دیگر ایفا میکند، بر کسی پوشیده نیست. این صنعت هم اکنون با گردش مالی حدود ۹۰۰ میلیارد دلار در سال، دومین صنعت با گردش مالی بالا پس از صنعت نفت است. صنعت فولاد از صنایع پرمصرف انرژی در سطح جهان به شمار میآید و حدود ۲۰ درصد از انرژی بخش صنعت را مصرف میکند. با توجه به اهمیت صنعت فولاد و مصرف بالای انرژی در فرآیند تولید آن، بهینهسازی مصرف انرژی در این صنعت بیش از پیش مورد توجه قرار گرفته است. با توجه به کاهش ظرفیت تولید گاز در سالهای آینده و نیز افزایش فزاینده مصرف گاز در کشور، ناترازی گاز به یکی از چالشهای تهدیدکننده امنیت انرژی کشور بدل خواهد شد. چالش ناترازی گاز در کشورمان، چالشی اساسی برای شرکتهای زنجیره فولاد نیز است. هم اکنون نیز در فصول سرد سال که مصرف گاز کشور بالا میرود، اولویت قطع گاز کشور با صنایع فولادی است. این مساله منجر به کاهش تولید و بروز زیان در واحدهای تولیدی این صنعت میشود. مصرف ویژه انرژی اولیه برای تولید فولاد در کورههای قوس الکتریکی فعال در کشور تقریبا چهار برابر فرآیند کوره بلند است. شرکتهای فولاد مبارکه اصفهان و فولاد خوزستان به دلیل تولید فولاد در کورههای قوس الکتریکی، انرژی بیشتری نسبت به شرکت ذوبآهن اصفهان مصرف میکنند. تولید شمش فولاد به روش کوره بلند محدود به شرکت ذوبآهن اصفهان است. تولید فولاد در کورههای الکتریکی (القایی و قوس) به دلیل بهرهمندی از یارانه گاز طبیعی و انرژی برق در طول زنجیره ارزش، در ایران بسیار سودده است و برخلاف کوره بلند، تبدیل گندله به آهن اسفنجی با مصرف گاز طبیعی در واحدهای احیای مستقیم انجام میشود.
عملکرد مصارف گاز در صنعت فولاد نشان میدهد این صنعت سهم بیشتری از رشد تولید گاز سبک را در مقایسه با دیگر صنایع عمده به خود اختصاص دادهاند و گاز طبیعی نقش موثری در رشد این صنعت دارد. بهینهسازی مصرف انرژی در صنعت فولاد در راستای رقابتپذیری این بخش صنعتی و نیز برای به حداقل رساندن تاثیرات محیطزیستی مانند انتشار گازهای گلخانهای حیاتی است. صنعت فولاد به طور متوسط پنج درصد از کل گاز تولیدی کشور را مصرف میکند، اما ظرفیت زیادی برای صرفهجویی مصرف گاز به عنوان اصلیترین انرژی مصرفی صنعت فولاد دارد که در این تحقیق به آن پرداخته میشود. نظر به اهمیت موضوع مورد بررسی، این تحقیق درصدد تبیین راهکارهای مدیریت مصرف گاز در صنایع عمده با تاکید بر صنعت فولاد کشور است.
بررسی وضعیت مصرف گاز در صنعت فولاد
همانطور که در نمودار شماره یک مشاهده میشود، ۷۲ درصد از انرژی مصرفی در صنایع آهن و فولاد کشور به گاز طبیعی اختصاص دارد. برق و کک نیز به ترتیب با ۲۰ و ۸ درصد، رتبههای ۲ و ۳ مصرف انرژی صنعت فولاد را به خود اختصاص دادهاند. مصرف گاز صنعت فولاد ایران در حال حاضر ۱۱ میلیارد مترمکعب در سال است و برای چند سال آینده در راستای تحقق اهداف سند چشمانداز سال ۱۴۰۴ این صنعت، مصرف گاز صنعت فولاد باید به بالای ۲۰ میلیارد مترمکعب برسد. بررسی روند مصارف گاز در صنعت فولاد از سالهای ۱۳۹۵ تا ۱۳۹۹ بیانکننده رشد سالانه حدود ۷/۱۳ درصد است در حالی که میانگین رشد سالانه مصرف گاز در صنایع پتروشیمی و سیمان یادشده در دوره به ترتیب ۱/۸ و ۵/۵ درصد بوده است. همچنین، میانگین رشد تحویل گاز سبک به خطوط سراسری گاز ۲/۵ درصد است بیشترین مقدار گاز مصرفشده (بیش از ۷۵ درصد) در فرآیند تولید آهن اسفنجی بوده است.
بر اساس عملکرد تولید فولاد در سال ۱۳۹۹، برای تولید هر تن شمش فولاد در کورههای قوس الکتریکی، القایی و کوره بلند به ترتیب ۴۲۵، ۲۲۰ و ۲۷ مترمکعب گاز طبیعی و ۱۱۳۵، ۸۲۵ و ۵۳۵ کیلووات ساعت برق در طول زنجیره ارزش مصرف شده است. بررسیها نشان میدهد از حدود ۴ دهه قبل تاکنون، میزان مصرف انرژی به ازای هر تن فولاد به خاطر تحقیقات انجام شده و فناوریهای جدید به کار رفته، روند نزولی داشته و حدود ۵۰ درصد کاهش یافته است؛ البته میزان انرژی مصرفی در واحدهای فولادسازی به نوع روش تولید یعنی کوره بلند یا کوره قوس الکتریکی بستگی دارد.
یکی از عواملی که موجب شده است مصرف گاز در صنعت فولاد به شکل بیرویه افزایش یابد، پایین بودن سهم هزینه انرژی در کل هزینهای تولید این صنعت است. هم اکنون حدود ۳/۳ درصد از هزینههای تولید در صنایع آهن و فولاد مربوط به هزینه مصرف انرژی است. این میزان در روش کوره قوس الکتریکی که بیشترین مصرف گاز را دارد، حدود ۱۰ درصد است. مثلا برای واحدی که خطوط گندلهسازی، احیای فولادسازی را در زنجیره تولید دارد، برای تولید هر تن گندله حدود ۲۰ مترمکعب گاز و حدود ۵۰ کیلووات ساعت برق، برای تولید هر تن آهن اسفنجی از گندله حدود ۳۵۰ مترمکعب گاز و حدود ۱۲۰ کیلووات ساعت برق و برای هر تن شمش از آهن اسفنجی حدود ۱۵ مترمکعب گاز و حدود ۸۳۵ کیلووات ساعت برق مصرف میشود. با در نظر گرفتن ضرایب تبدیل، میتوان به عدد ۷ درصد از کل هزینه تولید رسید.
به طور کلی، طرحهای افزایش تولید و عرضه گاز زمانبر است و نیاز به تامین مالی شایان توجه دارد. طبق برآورد شورای عالی انرژی برای افزایش تولید گاز از میادین جدید، به سرمایهای معادل ۵۰ میلیارد دلار نیاز است که در صورت جذب این سرمایه، اهداف تولیدی محقق میشود. بنابراین، تمرکز بر اجرای سیاستهای بهینهسازی و صرفهجویی مصرف گاز ضرورتی اجتنابناپذیر است. با توجه به طرحهای در حال اجرا از سوی صنعت فولاد، پیشبینی میشود تا سال ۱۴۰۴ به طور میانگین سالانه بیش از ۵ درصد، مصرف گاز صنعت فولاد افزایش یابد. سهم فرآیند تولید آهن اسفنجی از مجموع افزایش مصارف گاز تا سال ۱۴۰۴، حدود ۸۳ درصد خواهد شد. از سال ۱۴۰۴ به بعد، سقف مجموع گاز قابل تخصیص به صنعت فولاد حدود ۴۲ میلیون مترمکعب در روز لحاظ شده است و مازاد گاز مورد نیاز این صنعت باید از محل اصلاح و بهینهسازی تامین شود.
بررسی ظرفیت کاهش مصرف انرژی در صنعت فولاد به تفکیک زیربخشهای مختلف این صنعت نشان میدهد کاهش مصرف گاز طبیعی طبق استاندارد معیار مصرف انرژی در بخش فولاد، به طور متوسط ۲ درصد کاهش سالانه تا سال ۱۴۱۰ در نظر گرفته شده است. بر این اساس، مجموع مصرف انرژی در این صنعت بر اساس معیار بهترین مصرف انرژی، ۴۲۲ مترمکعب بر تن است که نسبت به وضعیت موجود ۶۲۰ مترمکعب بر تُن، حدود ۳۲ درصد ظرفیت صرفهجویی مصرف انرژی را نشان میدهد. بر اساس برآوردهای صورت گرفته در سند تراز گازی کشور تا افق سال ۱۴۲۰، کورههای احیا در صنعت فولاد با سهم ۵۱ درصد، بیشترین ظرفیت کاهش مصرف انرژی (گاز) را در بین دیگر بخشهای این صنعت دارند. بنابراین، اولویت سرمایهگذاری برای بهینهسازی مصرف انرژی در این صنعت با کورههای بلند است. بخشهای نورد و قوس الکتریکی نیز در اولویتهای بعدی قرار دارند.
ملاحظات امنیت انرژی
گاز طبیعی هماکنون مهمترین حامل انرژی در سبد تولید و مصرف انرژی کشور است و پیشبینی میشود سهم آن در سبد انرژی کشور افزایش بیشتری داشته باشد. با وجود برخورداری کشور از ذخایر عظیم گازی و افزایش تولید در سالهای اخیر، به دلیل دو روند نامطلوب یعنی ۱) افزایش نامتعارف مصرف داخلی گاز و ۲) افت تولید گاز در میدان پارسجنوبی به عنوان اصلیترین میدان گازی کشور (با سهم ۷۵درصدی از کل تولید گاز کشور)، تراز گازی کشور هماکنون در ۴ ماه سرد سال دچار کسری شده که قطعی گاز و برق در زمستان چند سال اخیر نمونهای از این روند نامطلوب گازی است. بر اساس سند تراز تولید و مصرف گاز طبیعی در کشور تا افق سال ۱۴۲۰، پیشبینی میشود با روند کنونی تولید و مصرف گاز، کشورمان در سال ۱۴۲۰ به واردات ۵۱۲ میلیون مترمکعب گاز در روز نیاز خواهد داشت. با توجه به وابسته بودن اغلب بخشها و صنایع کشور به گاز طبیعی، این مساله یکی از تهدیدات اصلی امنیت انرژی کشور در سالهای آینده است.
با توجه به اهمیت گاز در تولید آهن اسفنجی و اینکه رشد صنعت فولاد کشور مبتنی بر تولید آهن اسفنجی است، چالش کمبود گاز تاثیر منفی شدیدی بر صنعت فولاد ایران میگذارد. بر اساس سیاستهای فعلی، اولویت قطع گاز در مواقع کمبود با صنایع فولاد و آهن است. از این رو قطع گاز این صنایع روند تولید فولاد کشور را به مخاطره میاندازد. با توجه به دسترسی به حاملهای انرژی با قیمتهای یارانهای، قیمت تمام شده تولید فولاد در کورههای الکتریکی در ایران بسیار پایین است. این موضوع سبب شده است که بهرهمندی تولیدکننده از یارانه انرژی متناسب با مصارف ویژه انرژی در طول زنجیره ارزش باشد. بنابراین، عدم اصلاح تعرفه قیمتگذاری گاز متناسب با مصرف آن در صنایع، تهدیدی جدی بر فعالیت کل زنجیره این صنایع کلیدی است. گفتنی است، صنایع فولاد و آهن از آن جهت که تامینکننده زنجیره تولید دیگر صنایع نیز هستند، هرگونه اختلال در تولید این صنایع امنیت اقتصادی کشور را با مخاطره جدی مواجه میکند.
راهکارهای سیاستی
سهم در حال افزایش گاز طبیعی در سبد انرژی کشورمان و وابستگی بخشهای مختلف کشور به این حامل انرژی، توجه به مقوله مدیریت مصرف را بیش از پیش حائز اهمیت کرده است. هر ساله شاهد افزایش عمده سهم گاز در سبد انرژی و روند صعودی آن در بخشهای مختلف مصرف از جمله بخشهای صنعتی، تجاری، خانگی و نیروگاهی هستیم. مصرف رو به رشد گاز به گونهای است که با وجود ذخایر زیاد در کشور، مشاهده میشود در فصول سرد سال، اقدام به قطع گاز کارخانهها و شرکتهای داخلی و واردات آن برای رفع نیاز بخش خانگی میشود. صنایع فولاد و آهن از جمله صنایعی است که ظرفیت عمدهای برای صرفهجویی مصرف گاز دارد. قطع گاز نیز خسارتهای عدیدهای به این صنایع کلیدی کشور وارد میکند. برخی از راهکارهای پیشنهادی برای کاهش آسیبهای ناشی از مصرف بیرویه گاز و نیز ممانعت از بروز خسارت به این صنایع به شرح زیر است:
اصلاح و افزایش تعرفه سوخت واحدهای مصرفکننده بالاتر از معیار مصرف انرژی برای ترغیب واحدها به صرفهجویی در مصرف گاز: تغییر تعرفه قیمتگذاری گاز مصرفی در صنعت فولاد از راهکارهای قیمتی موثر بر ترویج انگیزه صرفهجویی مصرف انرژی به شمار میرود. هماکنون تنها ۳/۳ درصد از هزینههای تولید در صنعت فولاد مربوط به هزینه مصرف انرژی است. با توجه به سهم بسیار ناچیز هزینه سوخت از هزینههای تولید این صنعت، لزوم اصلاح پلکانی تعرفه سوخت واحدهای مصرفکننده انرژی (به ویژه گاز) برای ترغیب واحدهای تولیدی مذکور به صرفهجویی مصرف انرژی کاملا احساس میشود.
صرفهجویی مصرف انرژی با سرمایهگذاری در بهبود بازده انرژی برای تولید فولاد در کوره قوس الکتریکی: همانطور که در متن گزارش بررسی شد، چشمانداز تولید فولاد بر پایه بهینهسازی مصرف انرژی بنا شده است. بیشترین مصرف انرژی حرارتی گاز در صنعت فولاد مربوط به واحد احیای مستقیم و بیشترین مصرف انرژی الکتریکی نیز مربوط به کوره قوس الکتریکی است. بنابراین سرمایهگذاری در بهبود بازده مصرف گاز در این بخش کاملا ضروری است.
جلب همکاریهای بینالمللی برای افزایش سرمایهگذاری در راستای ارتقای فناوری تولید فولاد در کشور: تولید فولاد در کشورمان با وجود اینکه قدمت حدود نیم قرن دارد، کارایی تولید آن در کشور پایین و همراه با مصرف بالای انرژی است. جذب سرمایهگذاری خارجی همراه با بهکارگیری فناوریهای نوین میتواند زمینهساز توسعه صنعت فولاد ایران شود و کشور را برای دستیابی به جایگاه واقعی خود به طور جدی یاری دهد. اصلاح قوانین سرمایهگذاری، توسعه بندری، توسعه حملونقل دریایی، توسعه خطوط راهآهن و سرمایهگذاری در معادن سنگآهن ایران یو کشورها همسایه میتواند انگیزههای سرمایهگذاران خارجی را برای ورود به صنعت فولاد کشور به میزان زیادی افزایش دهد. یکی از زمینههای بالقوه جذب سرمایه، پروژههای ناتمام صنعت فولاد است. این پروژهها که به دلیل کمبود نقدینگی در مراحل ساخت دچار مشکل شده و از برنامه زمانی خود عقب افتادهاند، هزینه زیادی را به کشور تحمیل میکنند و در فرصت به دست آمده برای جلب سرمایهگذاری خارجی، لازم است این پروژهها در اولویت جذب سرمایههای خارجی قرار گیرند.
* پژوهشگر اقتصادی
اخبار برگزیدهاقتصاد کلانپیشنهاد ویژهلینک کوتاه :