غولهای سودسازی
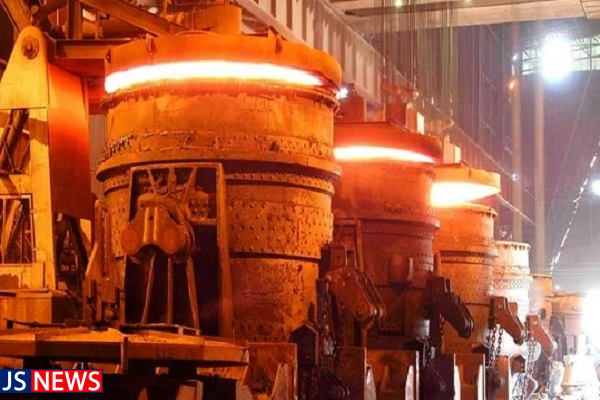
بررسیها نشان میدهد ظرفیت اسمی تولید محصولات فولادی در حدود ۴۲ میلیون تن است. تولید محصولات فولادی کشور در سال ۹۹ در حدود ۲۲ میلیون تن و در ۱۰ ماهه ابتدایی سال ۱۴۰۰، حدود ۴/۱۶ میلیون تن بوده است. ورق گرم و میلگرد بیشترین سهم تولید را در میان محصولات فولادی دارند. طبق آخرین آمار در دسترس برای سال ۱۴۰۰، میزان تولید محصولات فولادی نسبت به سال ۱۳۹۹ کاهش داشته است. وجود مشکلات قطعی برق در تابستان موجب شد که تولید محصولات فولادی نسبت به مدت مشابه سال قبل کاهش پیدا کند. گفتنی است ورق گرم به عنوان اصلیترین محصول فولادی در بازارهای جهانی مبادله میشود. در سالهای دورتر، میزان مصرف ورق گرم از میزان تولید بیشتر بود و مازاد تقاضای این محصول وارد میشد. اما پس از افزایش تولید، حجم تولید نسبت به مصرف پیشی گرفت و مقدار صادرات بیشتر از واردات شد. کشورهای امارات، عراق، افغانستان، چین، آفریقایجنوبی، تایلند، ایتالیا، ارمنستان، میانمار، سریلانکا، ترکمنستان، ازبکستان، ترکیه و پاکستان، اصلیترین مقاصد صادراتی انواع محصولات فولادی ایران هستند.
نیاز صنعت فولاد به تشکیل سرمایه ثابت ۱۱۸ هزار میلیارد تومانی
برای مصرف محصولات فولادی داخل کشور، در سالهای اخیر چشمانداز مصرف برای سال ۱۴۰۴ دستخوش تعدیل و تغییر شده است. آخرین برآورد، مصرف ۲۳ میلیون تنی محصولات فولادی در سال ۱۴۰۴ است که برای تحقق این مقدار مصرف، نیاز به تشکیل سرمایه ثابت ۱۱۸ هزار میلیارد تومانی با نرخ رشد متوسط پنج درصدی تا آن سال است. ملزومات تولید در این صنعت نیز هزینههای مشخصی دارند. اگر میزان انرژی لازم برای تولید فولاد در سال ۱۹۶۰، صد واحد فرض شود، هم اکنون این عدد به حدود ۴۰ واحد رسیده است. یعنی از سال ۱۹۶۰ تاکنون، ۶۰ درصد انرژی کمتری برای به وجود آمدن یک تن محصول فولادی صرف میشود. به طور کلی فولاد به دو روش کوره بلند و قوس الکتریکی تولید میشود. نوع انرژی لازم برای تولید فولاد به هرکدام از این دو روش، متفاوت است. در روش کوره بلند، میزان استفاده از زغالسنگ بیشتر است در حالی که در روش قوس الکتریکی سهم استفاده از گاز و برق در انرژی مصرفی بیشتر است. همچنین مقدار مصرف انرژی پنهان، شامل حملونقل مواد مصرفی از معادن در روش کوره بلند حدود ۹ درصد و در روش قوس الکتریکی حدود ۶ درصد از کل انرژی مصرفی را شامل میشود.
ملزومات تولید فولاد و چالشها
برای تولید فولاد بهرهمندی از برخی ملزومات ضروری است. در این میان دو انرژی گاز و برق و همچنین آب، به چالش جدی برای این صنعت طی سالهای اخیر بدل شده است. مصرف گاز در کشور به طور میانگین ۶۵۰ میلیون مترمکعب در روز است که در برخی از روزهای پرمصرف تا ارقام بالای ۸۰۰ میلیون تن نیز میرسد. برای تولید ۳۲ میلیون تن آهن اسفنجی در سال، ۲۹ میلیون مترمکعب در روز گاز نیاز است که علاوه بر این مقدار ۶ میلیون مترمکعب نیز در بخش گندلهسازی و ۶ میلیون مترمکعب در بخش نورد و فولادسازی مورد نیاز است. همچنین برای تولیدی معادل تولید سال ۹۹ صنعت فولاد کشور، نیاز به ۵۴۴/۳۳ میلیون کیلووات ساعت معادل ۶۶۵۵ مگاوات برق لازم بود که ۵/۷ درصد در بخش گندلهسازی، ۵/۱۱ درصد در بخش کنسانتره، ۱۲ درصد در آهن اسفنجی و ۶۷ درصد در تولید فولاد استفاده شده است. اگر تولید ادامه پیدا کند، در صورت نورد ورق ۱۸ درصد و نورد میلگرد و مقاطع ۱۶ درصد به مقادیر فوق افزوده میشود. ماده دیگر مورد نیاز برای تولید فولاد، آب است. مصرف آب به ازای تولید هر کیلوگرم فولاد، ۶/۵ لیتر به روش قوس الکتریکی و ۲/۵ لیتر به روش کوره بلند است.
در روش قوس الکتریکی از میزان ذکر شده، ۲۱ درصد در مرحله تولید کنسانتره، ۲ درصد گندله، ۲۷ درصد آهن اسفنجی و ۴۹ درصد در تولید فولاد خام استفاده میشود. در صورت ادامه دادن خط تولید تا محصولات فولادی، ۸/۲ لیتر در نورد ورق به روش سنتی، ۸/۱ لیتر در نورد ورق پیوسته و ۱/۱ لیتر در تولید مقاطع (به ازای تولید هر کیلوگرم) مورد نیاز است. در سال ۲۰۱۹، برای تولید ۸/۱ میلیارد تن فولاد در جهان، از حدود ۲ میلیارد تن سنگآهن، یک میلیارد تن زغالسنگ کک شو و ۵۷۵ میلیون تن آهن قراضه استفاده شد. آهن قراضه در سالهای اخیر به یکی از مهمترین اجزای تولید فولاد تبدیل شده است. آهن قراضه میتواند در روش تولید کوره بلند تا ۳۰ درصد و در روش تولید احیای مستقیم تا ۱۰۰ درصد محصول تولیدی نقش داشته باشد. در واقع هر کارخانه فولادی، یک نوع کارخانه بازیافت آهن نیز محسوب میشود. نرخ بازیافت آهن، یعنی میزان آهنی که پس از اتمام عمر دوباره به چرخه تولید برمیگردد در حدود ۸۵ درصد است. این رقم در مقایسه با نرخ بازیافت پلاستیک که در برخی مناطق کمتر از ۱۰ درصد است، رقم بالایی محسوب میشود. یعنی ۸۵ درصد از آهن محصولاتی که به اتمام عمر خود رسیده، یعنی ساختمانها، خودروها و…، بازیافت شده و در تولید دوباره فولاد نقش دارند. اگر ما برای محصولات آهنی، عمری حدود ۴۰ سال در نظر بگیریم، آهن قراضه ایجاد شده در سالهای آتی مشخص میشود. پیشبینی میشود که آهن قراضه در دسترس در سال ۲۰۳۰ به ۶۰۰ میلیون تن و در سال ۲۰۵۰ به ۹۰۰ میلیون تن برسد.
قیمت محصولات فولادی
محصولات فولادی بر حسب قیمتهای منطقهای فولاد خام و بر اساس میزان تغییری که روی فولاد خام اعمال میشود تا به مصرف نهایی برسد تعیین میشود. طبعا هر چه مراحل تولید طولانیتر باشد و افزودنیها و شکل محصول فولادی خاصتر باشد، محصول قیمت بالاتری دریافت میکند. یکی از مهمترین محصولات فولادی، ورق فولادی است که حجم تجارت و معاملات بالاتری دارد و کاربرد زیادی در صنایع پاییندستی دارد.
قیمت ورق داخلی ایران تحت تاثیر قیمتهای جهانی ورق است. در مقاطعی که تقاضا برای محصول داخلی بالا است، قیمت داخلی از قیمتهای اعلامی CIS بیشتر میشود. در ماههای اخیر این نرخ حوالی ۸۰۰ دلار بوده است. به گزارش سنا، عوامل اثرگذار در روندهای بلندمدت قیمت ورق گرم را میتوان اینچنین برشمرد: در سال ۲۰۰۹ تا انتهای ۲۰۱۱ کاهش شدید قیمت سنگآهن و زغالسنگ کک شو موجب شد که قیمت محصول از حدود ۶۸۰ دلار تا ۳۸۰ دلار کاهش پیدا کند. پس از آن سیاستهای اقتصادی دولت چین بعد از کاهش نرخ رشد اقتصادی به زیر ۷ درصد در پایان سال ۲۰۱۵ و در نتیجه تحریک بخشهای مصرفکننده فولاد از جمله بخش ساختمان و حملونقل و محدود کردن ظرفیت تولید از بزرگترین عوامل اثرگذار روی قیمت محصولات فولادی بودند. در سالهای بعد تنشهای تجاری آمریکا و چین و همچنین افزایش مالیات بر خرید خودرو در چین که منجر به کاهش تولید خودرو شد روی بازار فولاد اثر منفی گذاشت و در فصل اول ۲۰۲۰، با شروع بحران کرونا، کاهش قیمت در صنعت فولاد تشدید شد.
اما پس از آن با کاهش تنشهای تجاری چین و آمریکا، کاهش تولیدات در نتیجه همهگیری کرونا، بازگشت تدریجی تقاضا از فصل دوم ۲۰۲۰ و روند صعودی تولید خودرو در چین و افزایش تقاضا در بخش مسکن، موجب رشد قابل توجه قیمت محصولات فولادی بودند که در برخی مناطق قیمت ورق گرم تا حوالی ۲۰۰۰ دلار نیز بالا رفت. در ماههای اخیر نیز روند نزولی در قیمت شکل گرفته اما تنش موجود بین اوکراین و روسیه میتواند مجددا قیمتها را صعودی کند.
صنعت محصولات فولادی در بازار سرمایه
طی سالهای اخیر معمولا بازدهی گروه فولادی نسبت به بازار بهتر بوده است. همچنین در سالهایی که قیمت جهانی فولاد رشد داشته، این صنعت بازدهی بهتری ثبت کرده است. سطح فروش شرکتهای فعال در این صنعت تقریبا معادل میزان تولیدات آنها است و بر همین اساس برای پیشبینی مقدار فروش شرکتها، فرض شده است که موجودی کالای پایان دوره برابر با موجودی ابتدای دوره باشد.
برای پیشبینی نرخ فروش محصولات زنجیره نیازمند پیشبینی نرخ فروش ورق گرم هستیم. متوسط نرخ فروش ورق برای سال ۱۴۰۱ بهطور متوسط ۸۰۰ دلار در نظر گرفته شده است. برای دوره مذکور، متوسط نرخ تسعیر دلار برابر با ۰۰۰/۲۵ تومان لحاظ شده است که باعث میشود نرخ ریالی هر کیلو شمش در بورس کالا برابر با ۲/۲۱ هزار ریال باشد. همچنین، نسبت پایه برای نرخ گندله ۲۸ درصد و نرخ کنسانتره ۲۱ درصد نسبت به شمش در نظر گرفته شده است. برای سال آتی نیز قطعی برق احتمالی لحاظ شده است، با توجه به توضیحات ارائهشده، نسبت قیمت به درآمد پیشرو شرکتها در جدول محاسبه شده است.
از بزرگترین پتانسیلهای شرکتهای این گروه، میتوان به فروش در شرایط مختلف اقتصادی و سیاسی کشور، سایز نسبتا کوچک شرکتها، نسبت قیمت به سود مناسب، اهرم بالای شرکت به نرخ دلار و تسعیر با نرخ آزاد، صعود قیمتهای جهانی در مدت اخیر و دسترسی آسان به منابع اولیه اشاره کرد. همچنین برخی از شرکتهای گروه، دارای زمین و ساختمان ارزشمند هستند. از طرفی، ریسک قوانین و مقررات، افت شدید حاشیه سود در صورت کاهش قیمتهای جهانی، تخفیفات و قطعی گاز و برق، ریسکهایی هستند که در رابطه با شرکتهای این صنعت میتوان به آنها اشاره کرد.
لینک کوتاه :