از مونتاژ تا داخلیسازی
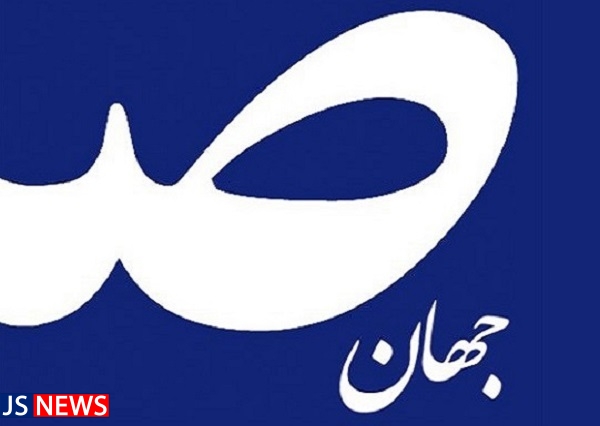
مهدی محمودی * طی سالهای اخیر و در پی خروج شرکتهای خارجی فعال در حوزه خودرو و همچنین قطع همکاری تامینکنندگان قطعات، شاهد کاهش تیراژ تولید خودرو و به دنبال آن افزایش روزافزون قیمتها در بازار بودهایم، به طوری که عرضه، تولید و خرید خودرو به عنوان یکی از کالاهای ضروری مردم دچار مشکلاتی شده است.
در این راستا برخی از اظهارنظرها از سوی کارشناسان مبنی بر وابستگی بیش از حد صنعت خودروی کشور به خارج و عدم کفایت بومیسازی اقلام مورد مصرف در این صنعت مطرح شد. کارشناسانی که عقیده داشتند این نقصان پس از ایجاد شرایط فعلی خود را در قالب کاهش تیراژ خودرو نشان داده است. به همین منظور برای بررسی چنین نظراتی لازم است به واکاوی سیر بومیسازی قطعات خودرو از اوایل دهه ۱۳۷۰ شمسی تاکنون پرداخته و برخی از زوایای مهم آن را مورد بررسی قرار دهیم. البته لازم به ذکر است که هدف از طرح این مطلب صرفا بررسی برخی از عوامل نه چندان مثبت به منظور آسیبشناسی و رفع آنهاست و در این رهگذر به هیچ عنوان نمیتوان تلاش شبانهروزی فعالان صنعت خودرو را در طول سالهای اخیر نادیده گرفت.
گام اول؛ افزایش تیراژ خودرو
پس از ظهور صنعت خودرو در کشور، شاهد افزایش تیراژ تولید آن در سالهای متوالی بودیم، به طوری که تیراژ تولید خودرو در سال ۱۳۴۹ از ۳۵ هزار دستگاه در سال به عدد ۱۶۱ هزار دستگاه تا قبل از شروع جنگ تحمیلی رسید. در طول سالهای جنگ تحمیلی نیز بنابر شرایط حاکم در کشور، صنعت خودرو دچار افت تولید شد، به طوری که در سال ۱۳۶۹ تولید آن تنها ۴۴ هزار دستگاه بود.
این شرایط سبب شد تا عملا صنعت خودروسازی کشور به حالت نیمهفعال درآید، تا حدی که زمزمههای جایگزینی اولویتهای دیگر به جای آن به گوش میرسید. در همین راستا بود که برای خروج از این وضعیت و فعال شدن مجدد این صنعت، نیاز به افزایش تیراژ تولید خودرو بود تا علاوه بر رفع نیاز داخلی، تولید اقتصادی خودرو نیز در دستور کار قرار بگیرد. بنا بر این دلیل روی تولیدات خودرویی آن زمان تمرکز شد که عمدتا خودروهای قدیمی محسوب میشدند.
با شروع دهه ۱۳۷۰ بحث واردات خودروهای خارجی به داخل کشور مطرح شد و در این رهگذر دو خودروساز بزرگ کشور نسبت به انتخاب شرکای فرانسوی و کرهای اقدام کردند. تا جایی که در ابتدا غالب قطعات به صورت CBU وارد و در داخل کشور مونتاژ میشد. البته با این روش بحث افزایش تیراژ خودرو امکانپذیر نبود و عملا راهی جز ایجاد تامینکنندگان داخلی و تقویت آنها برای دستیابی به تیراژ بالاتر وجود نداشت.
از آنجا که صنعت قطعهسازی کشور در آن سالها پتانسیل کافی را برای این موضوع نداشت، خودروسازان برای حمایت از آنها نسبت به ارائه پیشپرداختهای مناسب از محل عقد قراردادهای فیمابین اقدام کردند. در بدو امر تعداد محدودی از این شرکتها انتخاب شدند اما برخی از آنها پس از دریافت تسهیلات و پیشپرداختها راه خود را تغییر داده و به کارهای غیرمولد یا غیرخودرویی پرداختند که تبعات این موضوع خودروسازان را تا مدت زمان زیادی درگیر خود کرد. ولی در مقابل نیز اکثر تولیدکنندگان از این فرصت بهره جستند و با توجه به شرایط قیمت دستوری ارز و حجم تسهیلات دریافتی به واردات ماشینآلات صنعتی، ابزار و قالبهای مورد نیاز خود اقدام کردند که این امر باعث پایهگذاری اکثر صنایع قطعهسازی توانمند و فعلی در صنعت خودرو شد.
البته در آن زمان هدفگذاری صنعت خودرو افزایش تیراژ به واسطه ایجاد زنجیره تامین داخلی بود و تاکید و اصراری به تعمیق ساخت داخل به دلیل فقر دانش فنی و تکنولوژی وجود نداشت. لازم به ذکر است که این هدفگذاری از عامل مهم دیگری متاثر شده بود؛ اینکه خودروسازان خارجی به خصوص شرکت پژو در آن زمان به بازار بکر و مرغوبی دست پیدا کرده بودند و از سوی دیگر هیچکدام از آنها سرمایهگذاری در ایران انجام نداده بودند. بنابراین از آنجا که عواید و سود آنها ناشی از فروش قطعات بود، با بومیسازی قطعات آنها روزبهروز بازار خود را از دست میدادند و به صورت طبیعی نیز در مقابل این وضعیت مقاومت میکردند.
مقاومت شرکای خارجی برای بومیسازی قطعات
اولین شگرد خودروسازان خارجی در آن زمان مربوط به لیست شاخصهای ارزش جزء به جزء خودروی آنها یا اصطلاحا ایپیای (itemize price infices) بود. آنها قیمت قطعاتی که در آن زمان با سطح تکنولوژی آن روز امکان بومیسازی در داخل کشور را داشت بسیار پایین (حتی پایینتر از ارزش واقعی آن) در لیست فروش خود به خودروسازان داخلی قرار داده بودند. بنابراین در آن زمان خودکفایی قطعات بیشتر در حوزه قطعات پرسی، دکوراتیو خارجی مانند آیینهها و سپر و دکوراتیو داخلی همچون داشبورد و قطعات پلیمری داخل خودرو و صندلی اتفاق میافتاد که با خروج این اقلام پس از داخلیسازی، سود شرکت خارجی تغییر چندانی پیدا نمیکرد.
برعکس این موضوع، شرکای خارجی خودروسازان داخلی، قطعات با سطح تکنولوژی بالا که امکان ساخت داخل نداشت یا به سختی امکانپذیر بود را بسیار بالاتر از ارزش آن کالا در لیست فروش خود اعلام میکردند. از سوی دیگر در آن شرایط سرکوب قیمت ارز توسط دولتها، انگیزهای برای تولید قطعات به ویژه قطعات هایتک وجود نداشته و عملا واردات این اقلام نسبت به تولید داخلی آنها به صرفهتر بود. در نتیجه بومیسازی این اقلام، مخصوصا قطعات هایتک به شکل موفق صورت نگرفت و یا به عبارت صحیحتر زمینه و بستر مناسبی برای این امر وجود نداشت. به همین دلیل در بهترین شرایط اقلام به صورت CKD توسط قطعهسازان وارد و در داخل مونتاژ میشد که البته این اتفاق در آن زمان و شرایط در نوع خود ارزشمند بوده و جای تقدیر داشت. اما هر چند این موضوع یک قدم به سوی جلو محسوب میشد، اما در برخی موارد قطعات به صورت کامل (CBU) وارد شده و در اختیار خودروسازان قرار میگرفت.
رشد تا افول تولید
در این وضعیت در سال ۱۳۸۳ سازمان گسترش صنایع به منظور تولید پلتفرم مشترک بین دو خودروساز بزرگ کشور، نسبت به انعقاد قرارداد مشارکتی با شرکت فرانسوی رنو اقدام کرد که طی آن شرکتی با مشارکت رنو، سازمان گسترش صنایع، ایرانخودرو و سایپا برای تولید خودروی L90 تشکیل شد. در این خودرو نیز عواید شرکت رنو در فروش قطعات و اقلام تولید بود و بدیهی است که در بومیسازی قطعات، مقاومت وجود داشت. به طوری که اگر قطعهساز توانمند داخلی نسبت به انعقاد قرارداد بومیسازی اقدام میکرد، ملزم بود که مواد اولیه و برخی اقلام نیمهساخته خود را برای آن محصول از طرفهای قرارداد این خودروسازان از خارج کشور تامین کند. در غیر این صورت قطعات مورد تایید قرار نمیگرفت و عملا پروسه داخلیسازی کاری بسیار دشوار میشد. اگر هم داخلیسازی انجام میگرفت، منافع خودروسازان خارجی از طریق خرید اقلام نیمهساخته و یا مواد اولیه از شرکای خارجی آنها تامین میشد. به عنوان مثال در خصوص مواد اولیه پلیمری باید از تامینکنندگان خارجی طرف قرارداد این خودروسازان خارجی اقدام میشد و امکان تامین از منابع دیگر وجود نداشت. در غیر این صورت تاییدیه قطعه صورت نمیپذیرفت.
البته لازم به ذکر است، مجموع این عوامل و تمهیدات در افزایش تیراژ خودرو موثر بود و تیراژ تولید سالانه از ۴۴ هزار دستگاه در سال ۱۳۶۹ به ۲۱۸ هزار در سال ۱۳۷۹ و ۸۱۷ هزار دستگاه در سال ۱۳۸۴ افزایش یافت، ولی در اکثر موارد صنعت ما عمدتا در قطعات با سطح تکنولوژی بالا به واردکننده تبدیل شده و دانش فنی در حد مونتاژ محصولات وجود داشت. موضوع بعدی این است که در آن زمان در قطعات پیچیدهتر، قطعهسازان از فرصت به دست آمده و شرایط حاکم استفاده مناسب کرده و نسبت به انعقاد قرارداد با شرکتهای صاحب تکنولوژی در آن قطعات اقدام کردند. لیکن اکثر این قراردادها مربوط به خرید قطعه بود و شرکای خارجی از انتقال تکنولوژی (know How) امتناع میکردند و در بهترین حالت همانگونه که اشاره شد قطعات به صورت منفصله را در اختیار تولیدکنندگان داخلی قرار میدادند. به صورتی که معمولا تنها فرآیند مونتاژ در داخل انجام میشد و اجازه ساخت داخل صرفا برای قطعات پیش پا افتاده آن محصولات داده میشد.
بدیهی است با این سطح از دانش فنی، امکان تکوین محصول در خودروسازان و قطعهسازان وجود نداشت و عملا قطعات با سطح تکنولوژی بالا به صورت جعبه سیاه تلقی میشد، یعنی به جای اینکه قطعهسازان خارجی خود را با شرایط شرکای داخلی و به دنبال آن خودروسازان ایرانی تطبیق دهند، خواستههای خود را بر تولیدکنندگان داخلی تحمیل میکردند. به عنوان مثال اگر شرکت داخلی قطعهساز میخواست قطعهای را که به مرور زمان بستر تولید در داخل پیدا کرده و اقتصادی به نظر میرسید را بومیسازی کند، طرف قطعهساز خارجی از ارسال سایر قطعات امتناع کرده و یا به سختی قبول میکرد. البته همانگونه که اشاره شد قیمت دستوری و غیرواقعی ارز را نیز باید به این موضوع اضافه کرد که عملا واردات را در این رهگذر به صرفهتر میکرد.
پیامد تحریمها و رویکرد قطعهسازان
در نتیجه افزایش تیراژ خودرو با شرایط فوق ادامه پیدا کرد تا اینکه در سال ۱۳۹۰ با تحریمهای دور اول ایالات متحده در دولت باراک اوباما روبهرو شدیم. این شرایط جدید تیراژ خودرو را با توجه به خروج شرکای خارجی به شدت تحت تاثیر قرا داد، به طوری که تیراژ تولید خودرو که در سالهای ۱۳۸۹ و ۱۳۹۰، یک میلیون و ششصد هزار دستگاه در سال بود به ناگهان به نصف مقدار آن در سال ۱۳۹۱ کاهش یافت و عملا خودروسازان و قطعهسازان در تامین اقلام مورد نیاز خود دچار کمبود و محدودیت شدند. برخی از قطعهسازان تا قبل از شروع این دوره فعالیتهایی را در راستای بومیسازی قطعات خود انجام داده بودند، لیکن این مقدار از خودکفایی جوابگوی تیراژ تولید نبود. از سوی دیگر جهش ناگهانی قیمت ارز نیز واردات اقلام خودرویی را اگر به فرض امکانپذیر بود، عملا غیراقتصادی میکرد.
بنابراین جنبشی برای خودکفایی آغاز شد و نقطه عطف آن نیز خود را در تولید مجدد پژو ۲۰۶ نشان داد. به این دلیل که تا قبل از آن این خودرو تحت کنترل کارشناسان فرانسوی فرآیند بومیسازی خود را طی میکرد که بنا بر دلایلی که پیشتر ذکر شد، سرعت این بومیسازی بسیار کند بود و عملا قطعاتی مانند سیستم مالتی پلکس، سیستم تعلیق، ترمز، اقلام موتوری (بیشتر در ۲۰۶ و موتور tu3 (روند بسیار کندی در بومیسازی را طی کرده بود و یا عملا اتفاقی در این راستا صورت نگرفته و با خروج شرکت پژو تولید آن متوقف شده بود. این روند مثبت تا توافق برجام ادامه یافت، اما پس از این توافق بنابر دلایل مختلف از جمله سطح کیفی پایین قطعات بومیسازیشده و یا قیمت تمامشده قطعات با توجه به سرکوب قیمت ارز و یا عدم تیراژ مناسب، مجددا واردات برخی از قطعات عمدتا از سازندگان چینی از سرگرفته شد. هر چند که دستاوردهای بومیسازی قطعات نیز تا حد قابل قبولی حفظ شد و توسعه پیدا کرد.
از سوی دیگر روی کار آمدن دولت ترامپ در ایالات متحده و وضع تحریمهای مجدد، شوک بعدی را به صنعت خودرو وارد کرد و تیراژ خودرو را که عدد ۲/۱ میلیون دستگاه در سال ۱۳۹۵ و ۳/۱ میلیون دستگاه در سال ۱۳۹۶ را تجربه کرده بود، در سال ۱۳۹۷ به حدود ۹۳۷ هزار دستگاه تقلیل داد. در این شرایط بسیاری از تولیدکنندگان چینی نیز که سودای بازارهای اروپا یا آمریکا را در سر داشتند و یا اینگونه وانمود میکردند از همکاری با تولیدکنندگان ایرانی سرباز زده یا با واسطه به همکاری خود ادامه دادند؛ امری که منجر به افزایش قیمت تمامشده قطعات میشد. در همین رابطه بود که اهمیت بومیسازی بیش از پیش احساس شد.
در همین راستا، اینبار نوع خودکفایی عمدتا در مسیر درست خود نسبت به دفعات قبلی قرار گرفته بود. یعنی از آنجا که تحریمها بیشتر اثر خود را روی قطعات هایتک نشان میداد، شرکتهای توانمند داخلی روی این موضوع بیش از پیش تمرکز کردند. به طوری که اقلام با تکنولوژی بالایی مانند واحد کنترلکننده موتور (ECU)، واحد کنترلکننده ایربگ (DCU)، قطعات جانبی موتور (EMS)، فعالکننده ایربگ، سیستم مالتی پلکس و سایر اقلام از این دست به خودکفایی در داخل کشور رسید و ریشه این موضوع ایجاد هسته دانش در شرکتهای توانمند داخلی بود که اینبار را از دفعات قبلی متمایز میکرد.
دورنمای صادرات در صورت رفع موانع
در این رابطه لازم به ذکر است همانطور که توضیح داده شد، خودکفایی و بومیسازی دارای عمق کافی نبود و عملا دانش آن به صورت سطحی ایجاد شده بود، اما در خودکفایی قطعات هایتک مساله کاملا متفاوت است. به طوری که بدون ایجاد هسته دانش و استفاده از ظرفیتهای بالای متخصصان داخلی این امر امکانپذیر نبود و به ثمر نمینشست. به همین دلیل به طور قطع در حال حاضر با توجه به دانش فنی ایجادشده که به مرور در حال تکمیل است، شاهد ارتقای کیفی و کمی قطعات بومیسازی شده و به روز شدن این صنعت به شرط ادامه چنین فرآیندی خواهیم بود.
شرط ادامه این فرآیند نیز علاوه بر عزم جدی، نیازمند رفع برخی از موانع و تغییر نگرش صنعتی در این راه است. یعنی با توجه به اینکه افزایش تیراژ تولید قطعات بومی شده و ارتقای کیفی آنها با توجه به رفع موانع موجود مورد نیاز است، قطعا با فراهم شدن بسترهای مناسب در آیندهای نزدیک دستیافتنی بوده و حتی میتوان به صادرات بازارهای جدید نیز فکر کرد.
کارشناس صنعت خودرو
اخبار برگزیدهیادداشتلینک کوتاه :